Browsing the World of Fasteners and Machining: Techniques for Accuracy and Speed
In the detailed world of bolts and machining, the pursuit for accuracy and rate is a continuous challenge that demands thorough attention to information and critical preparation. From recognizing the diverse variety of bolt kinds to picking optimum products that can stand up to rigorous demands, each step in the procedure plays an essential duty in accomplishing the desired outcome. Precision machining methods further raise the complexity of this craft, requiring a delicate balance between technical knowledge and innovative techniques. As we look into the techniques that can boost both speed and performance in this domain, the interplay between quality control steps and functional quality becomes an important centerpiece.
Understanding Bolt Types
When choosing fasteners for a job, understanding the different types offered is essential for ensuring optimum performance and integrity. Fasteners can be found in a vast array of types, each created for details applications and demands. Screws are made use of with nuts to hold products together, while screws are flexible bolts that can be utilized with or without a nut, depending on the application. Nuts, on the various other hand, are inside threaded fasteners that mate with screws or screws, providing a secure hold. Washing machines are essential for dispersing the load of the fastener and stopping damages to the material being attached. Furthermore, rivets are long-term fasteners that are excellent for applications where disassembly is not needed. Understanding the differences in between these fastener types is necessary for picking the right one for the task, guaranteeing that the link is strong, resilient, and reputable. By picking the ideal fastener kind, you can maximize the efficiency and long life of your task - Fasteners and Machining.
Picking the Right Products
Recognizing the value of picking the best products is extremely important in guaranteeing the optimum efficiency and integrity of the picked fastener types talked about previously. When it involves bolts and machining applications, the product selection plays an important function in identifying the general strength, durability, corrosion resistance, and compatibility with the desired atmosphere. Different products offer differing properties that can substantially influence the efficiency of the bolts.
Typical materials made use of for fasteners include steel, stainless-steel, light weight aluminum, titanium, and brass, each having its special toughness and weak points. Steel is renowned for its high toughness and toughness, making it suitable for a wide variety of applications. Stainless steel supplies excellent corrosion resistance, ideal for settings susceptible to moisture and chemicals. Aluminum is lightweight and corrosion-resistant, making it appropriate for applications where weight decrease is important. Brass is usually selected for its aesthetic appeal and excellent conductivity. Titanium is understood for its phenomenal strength-to-weight proportion, making it ideal for high-performance applications. Picking the best product entails taking into consideration variables such as strength needs, ecological problems, and budget plan restrictions to ensure the wanted performance and durability of the fasteners.
Precision Machining Techniques
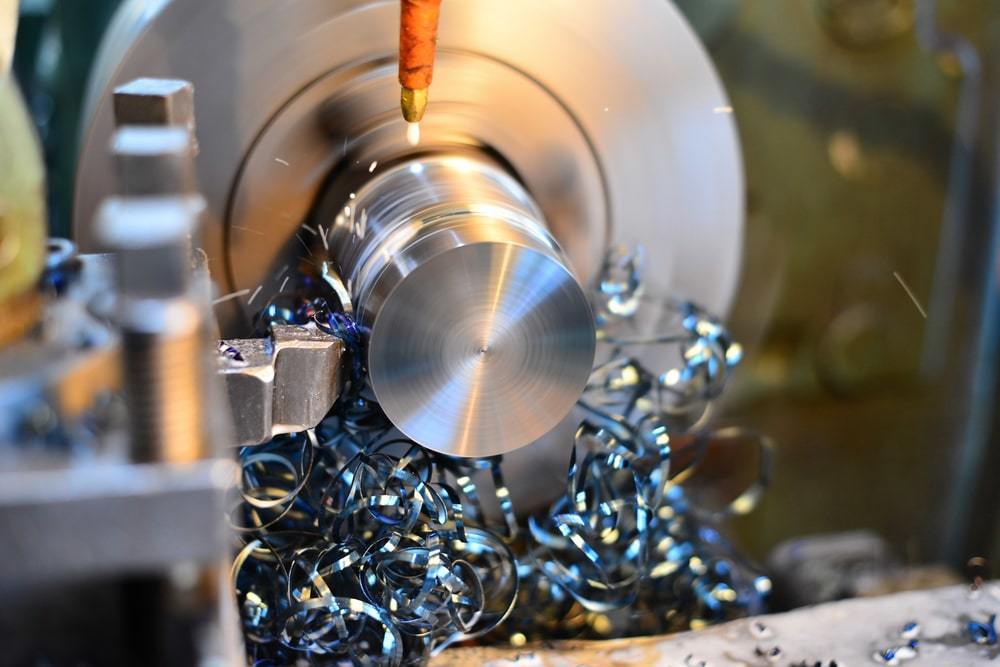
Along with CNC machining, other precision methods like grinding, turning, milling, and boring play essential functions in fastener manufacturing. Grinding helps achieve great surface finishes and tight dimensional resistances, while transforming is frequently utilized to develop round elements with precise sizes. Milling and boring procedures are necessary for forming and creating openings in fasteners, ensuring they meet precise specs and function properly.
Enhancing Speed and Performance
To maximize fastener manufacturing procedures, it is vital to simplify procedures and implement reliable techniques that enhance precision machining methods. One crucial technique for improving rate and performance is the execution of lean manufacturing principles. By lowering waste and focusing on continuous enhancement, lean techniques aid maximize and get rid of bottlenecks workflow. Furthermore, purchasing automation innovations can dramatically boost production rate. Automated systems can handle repetitive jobs with precision and rate, allowing workers to concentrate on even more complex and value-added tasks. Embracing Just-In-Time (JIT) stock management can likewise enhance effectiveness by making sure that the appropriate materials are readily available at the correct time, decreasing excess inventory and lowering preparations. In addition, fostering a society of partnership and communication among employee can improve overall efficiency by promoting transparency, analytical, and development. By combining these methods, makers can accomplish a balance in between speed and accuracy, eventually enhancing their affordable side in the bolt market.
Top Quality Control Actions
Carrying out extensive top quality control measures is essential in ensuring the integrity and consistency of bolt products in the production process. Fasteners and Machining. Quality control actions incorporate different stages, starting from the selection of raw materials to the last inspection of the finished bolts. This includes examining elements such as material stamina, longevity, and make-up to ensure that the bolts meet sector requirements.
Normal calibration of tools and equipment is necessary to preserve consistency in manufacturing and make sure that fasteners satisfy the necessary resistances. Implementing stringent protocols for recognizing and attending to his response flaws or non-conformities is vital in avoiding substandard items from entering the market. By developing an extensive high quality control structure, producers can support the track record of their brand and provide fasteners that meet the highest possible criteria of efficiency and durability.
Verdict
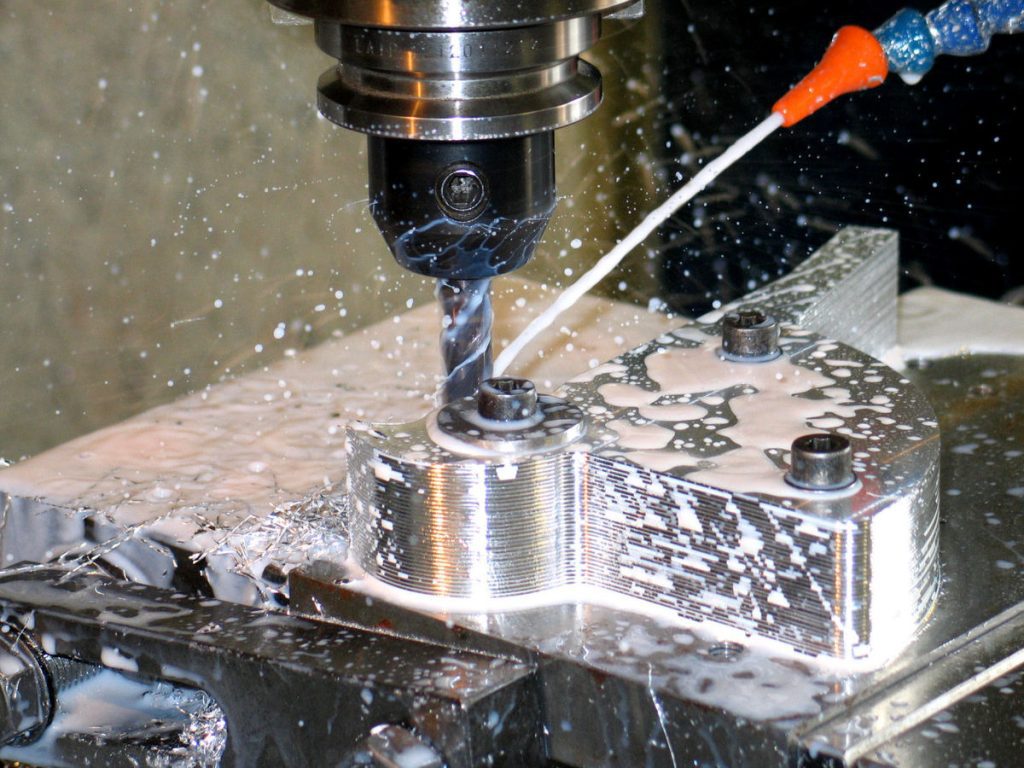
In the elaborate realm of fasteners and machining, the pursuit for precision and speed is a continuous obstacle that demands precise attention to information and critical planning. When it comes to bolts and machining applications, the product choice plays a crucial role in identifying the overall toughness, longevity, corrosion resistance, and compatibility with the designated setting. Accuracy machining includes various innovative methods that guarantee the tight resistances and specs needed for fasteners.In addition to CNC machining, other precision techniques like grinding, turning, milling, and boring play important duties in bolt production.To optimize bolt manufacturing processes, it is crucial to streamline procedures and apply efficient strategies that enhance accuracy machining methods.
Comments on “Ingenious Fasteners and Machining Solutions for Complicated Styles”